How Artificial Intelligence in Industrial Automation Improves Efficiency & Productivity
The manufacturing landscape is undergoing a profound transformation as artificial intelligence in industrial automation revolutionizes how factories operate. Today’s smart factories leverage AI to predict issues before they occur, optimize processes in real-time, and adapt to changing conditions without human intervention. This technological revolution isn’t just changing what’s possible—it’s redefining what’s expected in modern manufacturing.
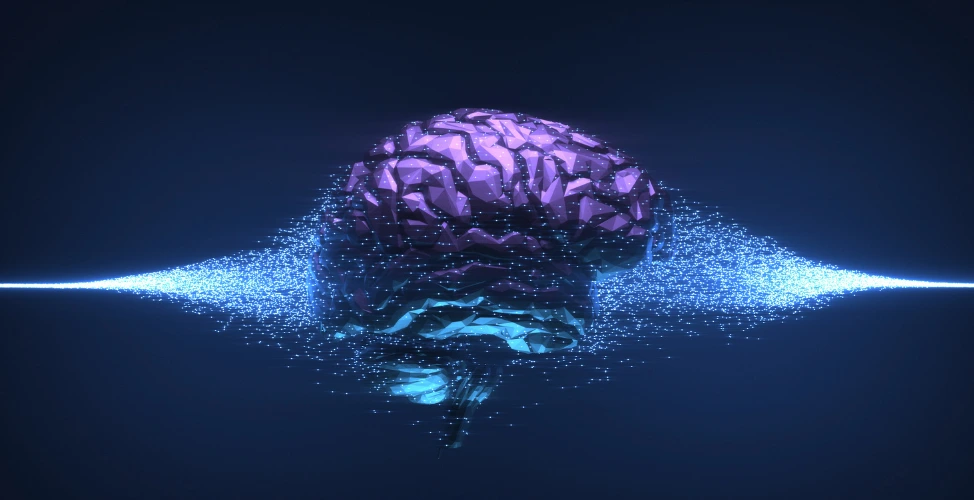
What is Artificial Intelligence in Industrial Automation
Artificial intelligence in industrial automation represents the integration of AI technologies into manufacturing systems to enable machines to perform complex tasks, learn from experience, and make decisions with minimal human intervention. Unlike conventional automation, which executes pre-programmed instructions, AI-powered systems can analyze data, identify patterns, adapt to new situations, and continuously improve their performance.
Fundamental differences between traditional and AI-driven automation
The contrast between conventional automation and artificial intelligence in industrial automation goes beyond incremental improvement—it represents a paradigm shift. Traditional automation excels at repetitive, predictable tasks within controlled environments but struggles with variability. These systems follow explicit programming and cannot adapt to unexpected situations without human intervention. When conditions deviate from the norm, production typically halts until engineers can resolve the issue.
Perhaps most significantly, artificial intelligence in industrial automation enables predictive capabilities that transform maintenance and quality control from reactive to proactive disciplines. At a pharmaceutical packaging facility in Ireland, an AI system accurately predicted equipment failures 97% of the time, with an average of 8.5 days advance notice—sufficient time to schedule maintenance during planned downtime rather than experiencing costly production interruptions.
Read more: 15 eCommerce Marketing Automation Software to Enhance Growth
Key Benefits of Artificial Intelligence in Industrial Automation
The implementation of artificial intelligence in industrial automation delivers tangible benefits that directly impact an organization’s bottom line while simultaneously improving product quality, worker experiences, and environmental sustainability. These advantages extend far beyond simple efficiency gains to create competitive advantages that are difficult for non-AI-equipped competitors to match.
Reduction in downtime and maintenance costs
Unplanned downtime represents one of manufacturing’s most significant expenses, with costs averaging $260,000 per hour in automotive manufacturing. Artificial intelligence in industrial automation dramatically reduces these incidents through predictive maintenance strategies that identify potential failures before they occur. AI systems continuously monitor equipment health through sensors that detect temperature fluctuations, vibration patterns, acoustic signatures, and other indicators invisible to human operators.
At a paper mill in Finland, implementing AI predictive maintenance reduced unplanned downtime by 82% within the first year of deployment. The system analyzed historical failure data alongside real-time sensor information to create sophisticated failure prediction models for critical equipment. Maintenance teams now receive alerts weeks before likely failures, converting what would have been emergency repairs into planned maintenance activities. This transition from reactive to predictive maintenance through artificial intelligence in industrial automation reduced the mill’s maintenance costs by €3.8 million annually while extending equipment lifespan by an average of 23%.
Enhanced precision and consistency in manufacturing
Manufacturing quality depends on consistency—producing identical products regardless of external variables. Artificial intelligence in industrial automation excels at maintaining precise process control despite fluctuations in raw materials, environmental conditions, or equipment wear. AI terms systems continuously adjust parameters in real-time to compensate for these variations, ensuring consistent output quality that would be impossible with traditional automation.
A semiconductor manufacturer in Taiwan implemented AI-controlled lithography processes that reduced nanoscale variation by 72%, dramatically improving yield rates for their most advanced chips. The system analyzes millions of data points to make microsecond adjustments to exposure times, temperatures, and chemical concentrations. This application of artificial intelligence in industrial automation enabled production of components with features measuring just 3 nanometers—about 1/30,000th the width of a human hair—with unprecedented consistency. The economic impact was substantial: a 9% improvement in yield translated to approximately $42 million in additional revenue annually from a single production line.
Real-time performance monitoring and analysis
Traditional performance monitoring involves periodic sampling and retrospective analysis, often identifying issues after significant waste has accumulated. Artificial intelligence in industrial automation transforms this approach by enabling continuous, comprehensive monitoring across all production parameters simultaneously. These systems don’t merely track metrics—they understand complex interrelationships between variables and identify optimization opportunities humans might miss.
A beverage bottling operation deployed an AI monitoring system that analyzes 27,000 data points per second across its filling lines. The system identified subtle correlations between ambient humidity, carbonation levels, and filling valve performance that were causing inconsistent fill levels. By automatically adjusting parameters based on these insights, artificial intelligence in industrial automation reduced overfilling by 42%, saving approximately 98,000 liters of product monthly. The system’s ability to detect and correct inefficiencies in real-time eliminated the delay between problem identification and resolution that characterizes traditional monitoring approaches.
How to Apply Artificial Intelligence in Industrial Automation?
Artificial intelligence in industrial automation is opening up new possibilities for smarter, faster, and more efficient production environments. AI technologies can analyze massive volumes of real-time data, enabling systems to adapt to changes instantly and optimize workflows with minimal human intervention.
One practical way to drive AI digital transformation in manufacturing is through predictive maintenance. By using sensors and machine learning algorithms to monitor equipment in real time, factories can detect potential issues before they lead to failures. This proactive approach minimizes unplanned downtime, extends the lifespan of machinery, and significantly reduces operational costs—highlighting how AI digital transformation enhances both efficiency and reliability in industrial environments.
AI can also improve quality control by detecting product defects that are invisible to the human eye. With computer vision and real-time feedback loops, manufacturers can ensure consistent product standards and minimize waste.
Additionally, AI enhances human-machine collaboration. Intelligent robots and co-bots can learn from their environments and adjust to new tasks without extensive reprogramming. This flexibility allows industrial operations to scale quickly and respond to market demands more effectively.
As AI continues to evolve, businesses that embrace it early in their automation strategies will gain a significant competitive advantage—driving innovation and long-term growth across the manufacturing sector.
Unlock Industrial Excellence with SmartOSC’s AI Automation Solutions
SmartOSC has established itself as a pioneer in implementing artificial intelligence in industrial automation across diverse manufacturing environments. Our solutions combine industry-specific expertise with cutting-edge AI capabilities to deliver measurable improvements in efficiency, quality, and profitability.
The company’s Industrial Intelligence Platform provides a comprehensive foundation for artificial intelligence in industrial automation initiatives. This scalable solution integrates with existing equipment through an extensive library of pre-built connectors, minimizing implementation complexity while maximizing value delivery. Their platform approaches each client’s challenges through a systematic methodology that begins with thorough assessment, proceeds through carefully staged implementation, and continues with ongoing optimization supported by their expert team.
SmartOSC’s AI-powered automation doesn’t just streamline workflows—it provides actionable insights through advanced analytics, enabling data-driven decision making across your organization. Our systems identify inefficiencies, recommend improvements, and implement solutions with minimal human intervention, allowing your team to focus on strategic initiatives rather than routine tasks.
Read more: The Future of Automative Software Development: AI, IoT & Cloud Integration
Conclusion
The integration of artificial intelligence in industrial automation represents not merely an evolutionary step but a revolutionary transformation of manufacturing capabilities. The future of industrial excellence is here, and SmartOSC is your trusted partner in this transformation journey. Contact us today for a personalized consultation and discover how our tailored AI automation solutions can drive productivity, reduce costs, and propel your business toward unprecedented success.