A Real-World Manufacturing Example in Supply Chain Management
Efficient supply chain work shapes modern manufacturing success. Many businesses still struggle with inventory hurdles, disconnected teams, or sluggish delivery processes. A smooth approach prevents chaos and raises competitiveness. Today, we will look at a manufacturing example in supply chain contexts and see how it elevates performance. Let’s begin by clarifying what supply chain management involves and why it matters so much.
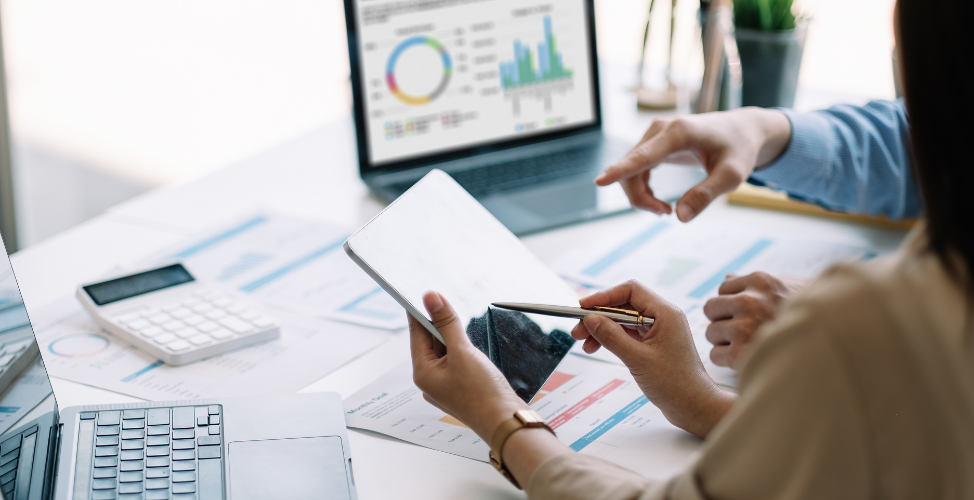
Understanding Supply Chain Management in Manufacturing
Supply chain management (SCM) oversees the entire lifecycle of a product—from sourcing raw materials to delivering finished goods to customers. It involves a complex network of suppliers, manufacturers, warehouses, and logistics providers that must work in sync to ensure efficiency. A common manufacturing example in supply chain includes coordinating material deliveries to factories just in time for production, helping avoid delays or excess inventory. However, disruptions such as material shortages or unexpected shifts in demand can occur, highlighting the importance of strong, responsive supply chain management practices.
What Is Supply Chain Management and How Does It Work?
Manufacturing teams need raw materials on time, in the right quantity, and at the right place. SCM addresses this by coordinating purchasing, scheduling, and logistics. Some plants run a ‘just-in-time’ model, meaning they hold minimal stock and depend on prompt deliveries. Others prefer a ‘safety stock’ plan, storing extra materials in case of hiccups.
A well-managed supply chain relies on seamless coordination and real-time visibility across every stage of production and distribution. Thanks to digital transformation in manufacturing, production teams can access accurate demand forecasts to plan output efficiently, while warehouse staff are notified exactly when materials will arrive. Simultaneously, transportation partners receive live updates to ensure on-time deliveries. This high level of synchronization is made possible by integrating advanced technologies, data analytics, and smart planning—helping manufacturers reduce delays, minimize backlogs, and maintain smooth, responsive operations.
Importance of Supply Chain Management in the Manufacturing Sector
SCM helps keep production costs predictable. Missed deliveries can force expensive rush orders or slow production lines, frustrating both staff and customers. Solid planning fosters stable output.
Even more importantly, it enhances product quality. A manufacturing example in supply chain would be a manufacturer closely monitoring suppliers to catch substandard materials early, preventing costly issues down the line. Improved coordination also helps reduce shipping delays, ensuring customers receive their orders faster. According to a recent KPMG survey of 250 U.S. executives, 81% expect most of their U.S.-serving supply chains to be based in the Americas after completing current transitions. This renewed focus on regional supply chains stems from the realization that disruptions can severely impact customer satisfaction and brand loyalty.
Watch more: What is Digital Manufacturing and Why is It the Future of Production?
Case Study: Apple’s Supply Chain Strategy
A widely known manufacturing example in supply chain circles is Apple Inc. The tech giant does not operate typical assembly lines under its direct control. Rather, it partners with multiple third-party manufacturers. That approach may seem risky, yet Apple’s results speak volumes.
Overview of Apple’s Manufacturing and Supply Chain Operations
Apple sets strict standards for its partners. It thoroughly audits material suppliers, chipmakers, and assembly lines scattered worldwide. Each component, from tiny screws to specialized chips, is tied to a detailed schedule. Apple carefully orchestrates volumes to avoid large surpluses and stale inventory.
Apple rarely relies on large warehouses filled with unsold inventory. Instead, the company adapts quickly to changing consumer preferences—an impressive manufacturing example in supply chain efficiency. This agility depends on highly accurate demand forecasting, where even a small error can lead to production slowdowns or excess stock. Apple addresses this by closely analyzing early preorders and adjusting manufacturing output in real time. Tim Cook, with his strong background in operations, has been instrumental in developing this lean, responsive supply chain model that minimizes waste while ensuring products are available when and where they’re needed.
Strategies Implemented by Apple
- Multi-Supplier Approach: Apple taps more than one source for key components. If one supplier faces a glitch, Apple shifts orders to others. This cuts the risk of single-point disruptions. Some years ago, a major tsunami threatened particular supplies, but Apple’s diverse network minimized production slowdowns.
- Close Collaboration: Apple invests in equipment and training for its contract manufacturers. In return, these partners commit to strict timetables. They also gain stable, high-volume orders. Apple’s oversight ensures each partner meets labor and safety guidelines.
- Robust Logistics: Apple arranges high-speed transport, including air freight, for newly released items. This keeps shelves stocked quickly across continents. Many watchers have noted how iPhones appear in multiple global markets almost simultaneously. That feat springs from Apple’s advanced logistic channels.
Outcomes and Benefits
This well-tuned chain has contributed to Apple’s strong margins. According to a recent Gartner report, Apple ranked near the top in supply chain masters for over five consecutive years. Meanwhile, Apple can ramp up production for new device launches with minimal notice. That agility cements brand reputation and keeps Apple fans returning.
Additionally, data from IDC indicates that Apple shipped 76.9 million iPhones in the fourth quarter of 2024, achieving a 23.2% market share.
This success highlights how a well-managed supply chain powers growth while curbing excess spending.
Lessons Learned from Apple – Manufacturing Example in Supply Chain
Apple’s example underscores practical ways to strengthen supply chain structures. Even if you produce car parts or medical devices, certain principles remain universal. Let’s check out how they apply.
Importance of Supplier Relationships
Mutual trust drives consistent quality. Frequent audits, fair contract terms, and transparent communication matter a great deal. When changes arise, both manufacturer and supplier should update each other fast. That fosters loyalty, especially during tight timelines.
Yet, it goes beyond signing a contract. Setting up clear metrics and escalation paths helps solve hiccups. If a supplier sees potential raw material shortages, they can alert the manufacturer so alternative plans start in time. This synergy helps both sides remain profitable.
Using Technology for Supply Chain Improvement
Technology enables real-time visibility across the entire supply chain. A manufacturing example in supply chain would be the use of RFID tags, IoT sensors, and smart software to monitor the movement of raw materials or finished goods. If a shipment is delayed unexpectedly, managers are alerted immediately and can reroute orders to avoid disruption. This level of transparency reduces guesswork, minimizes downtime, and helps maintain a smooth production flow.
One big leap has been data analytics. Systems now project demand, spot trends, and even handle dynamic scheduling. According to a Deloitte study, around 68% of manufacturing executives reported adopting advanced analytics to handle supply chain forecasts. That’s a sharp climb from pre-2020 figures. Those who harness such tools see fewer stockouts and better order accuracy.
Watch more: What is Supply Chain Management and Why is It Important for Businesses?
Risk Management and Diversification
No chain is perfect. Weather disasters, political tensions, or labor strikes can strike without warning. Having multiple suppliers or logistics partners lowers the chance that one breakdown derails everything. Apple’s multi-source approach is a hallmark, but smaller manufacturers can do it on a simpler scale.
Business continuity plans also help. Some keep backup stocks of vital parts or extra shipping routes. Others sign flexible contracts that allow quick scaling up or down. By staying ready, you dodge panic when disruptions pop up.
How SmartOSC Can Elevate Your Manufacturing Supply Chain
Running a strong supply chain takes skill, planning, and consistent refinement. That’s where SmartOSC steps in. We focus on advanced digital transformation solutions that sync factories, distributors, and retail channels under one roof.
Our team builds customized systems designed to streamline operations, reduce manual tasks, and provide real-time visibility across the supply chain. A manufacturing example in supply chain might involve seamlessly connecting procurement processes, inventory records, and shipping updates into one centralized platform. With just a few clicks, manufacturers can monitor and manage their entire workflow. By leveraging modern technologies and industry best practices, this integration brings greater speed, accuracy, and control to every stage of the supply chain.
In many cases, we integrate cloud-based platforms that highlight your stock levels, automate orders, and notify your team if any link falters. Our experts also offer insights on stable expansions or peak season readiness. That helps your brand adapt quickly without an overwhelming budget or heavy staff changes.
One example? Daikin Vietnam. They partnered with SmartOSC to digitize a clunky, paper-heavy process that slowed down their internal operations. Within six months, we helped them move 80% of workflows online, cutting paperwork by the same rate. Cloud-based approvals, task alerts, and real-time document tracking now keep their supply chain sharp and steady.
Not only that, but we support implementation from start to finish. Testing, staff training, and ongoing improvements all fall under our scope. It’s a ‘one-stop synergy’ that fosters growth in a practical, simple way. ‘Synergy’ aside, you get real results from streamlined operations.
Conclusion
A vibrant supply chain reduces waste and builds brand loyalty. From Apple’s multi-supplier model to real-time data systems, these approaches fit any manufacturing example in supply chain discussions. Good planning wards off delays, fosters collaboration, and boosts profits. Shorter lead times please customers and keep them loyal. Tighter relationships with suppliers protect production from abrupt shocks.
If you’re aiming for sharper processes and stable growth, consider technology upgrades, thorough collaboration, and long-range planning. You can also partner with an experienced group like SmartOSC to map out your journey. Want help applying these ideas to your own business? Contact us to start building a smarter supply chain with SmartOSC.