What Is Digital Manufacturing and Why Is It the Future of Production?
A Magento web development company is an agency specializing in building fully functional and highly effective online retail stores, using Magento open source code. If you are learning about a Magento agency or looking for an agency to build an online store, you can refer to the list below.
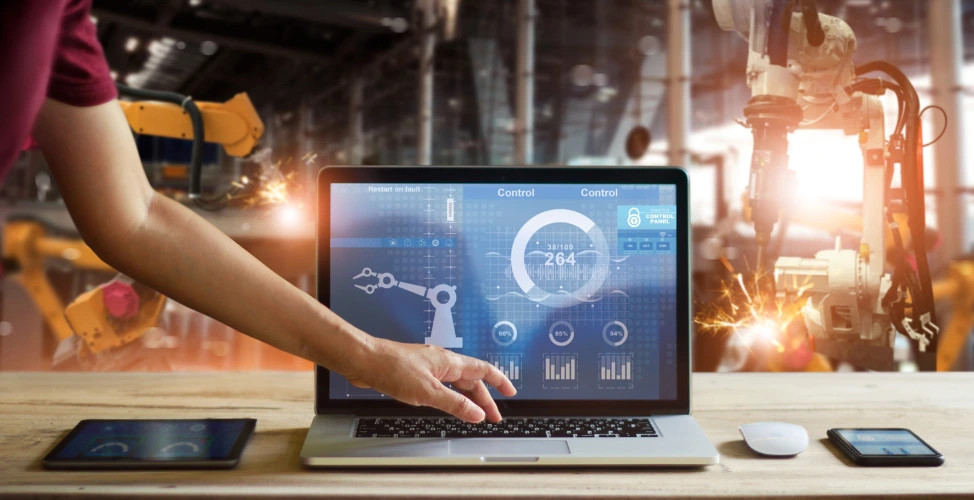
Defining and Core Components of Digital Manufacturing
Define: What Is Digital Manufacturing?
Digital manufacturing is a comprehensive approach to production that integrates advanced digital technologies across the entire manufacturing ecosystem. It’s far more than simply adding a few high-tech machines to a production line. What is digital manufacturing at its essence? It’s a holistic strategy that connects every aspect of manufacturing—from initial design to final product delivery—through intelligent, interconnected digital systems.
Digital transformation in manufacturing replaces fragmented, manual processes with a seamless, data-driven ecosystem where technology and human expertise collaborate effectively. Unlike traditional methods, this transformation turns manufacturing into a dynamic, intelligent system—capable of adapting quickly to shifting market demands. By integrating real-time data, automation, and smart technologies, digital transformation in manufacturing empowers businesses to operate with greater agility, precision, and efficiency than ever before.
Core Components: The Building Blocks of Digital Manufacturing
Understanding what digital manufacturing is requires a deep dive into its core technological components. These interconnected technologies work together to create a smart, efficient, and adaptive manufacturing ecosystem:
Internet of Things (IoT) Integration
IoT is the nervous system of digital manufacturing. Imagine sensors embedded throughout the production floor, continuously collecting and transmitting real-time data. These smart devices monitor everything from machine performance and environmental conditions to product quality and energy consumption. What is digital manufacturing’s most powerful IoT advantage? The ability to create a completely transparent and predictive manufacturing environment.
These IoT sensors enable:
- Real-time equipment monitoring
- Instant performance tracking
- Predictive maintenance alerts
- Comprehensive energy management
- Immediate quality control interventions
Advanced Robotics and Automation
Robotics in digital manufacturing goes far beyond simple repetitive tasks. Modern manufacturing robots are intelligent, adaptable, and capable of complex operations with remarkable precision. What is digital manufacturing’s robotics approach? It’s about creating collaborative environments where robots and human workers complement each other’s strengths.
Advanced robotics offer:
- Unprecedented precision in manufacturing
- Ability to handle complex, multi-step processes
- Reduced human error
- Increased production speed
- Capability to work in challenging environments
Artificial Intelligence and Machine Learning
AI and machine learning are the brains behind digital manufacturing’s intelligence. These technologies analyze vast amounts of data to identify patterns, predict outcomes, and continuously optimize manufacturing processes. What is digital manufacturing’s AI potential? It’s the ability to learn, adapt, and improve manufacturing strategies in real-time.
Key AI capabilities include:
- Predictive maintenance scheduling
- Quality control optimization
- Production process optimization
- Supply chain management improvements
- Advanced demand forecasting
Cloud Computing and Big Data Analytics
Cloud computing and big data analytics provide the infrastructure and intelligence that power digital manufacturing. These technologies enable manufacturers to store, process, and analyze massive amounts of data from across the production ecosystem. What is digital manufacturing’s data advantage? The ability to transform raw data into actionable insights that drive strategic decision-making.
Benefits include:
- Scalable computational resources
- Global collaboration capabilities
- Advanced data analysis
- Secure data storage and management
- Real-time performance tracking
Read more: Digital Transformation Solutions: Navigating the Future of Business
Why Digital Manufacturing Is the Future: Key Benefits
Enhanced Productivity and Operational Efficiency
Digital manufacturing revolutionizes productivity through multiple transformative mechanisms. Traditional manufacturing often struggles with inefficiencies, manual interventions, and fragmented processes. In contrast, digital manufacturing creates a fully integrated ecosystem where every aspect of production is optimized in real-time.
Productivity enhancements come from several critical improvements:
- Automated workflow management reduces human bottlenecks
- Real-time data analytics identify and eliminate production inefficiencies
- Intelligent scheduling optimizes machine utilization and resource allocation
- Continuous performance monitoring enables immediate process adjustments
- Reduced manual data entry and tracking minimizes human error
For example, manufacturers using digital manufacturing technologies have reported productivity increases of 15-30% within the first year of implementation. Smart sensors and IoT devices can track equipment performance down to milliseconds, identifying potential slowdowns before they impact production lines.
Improved Product Quality and Consistency
What is digital manufacturing? It’s a modern approach that transforms quality control from a reactive step to a proactive, integrated process. Unlike traditional methods where checks happen only after production—risking the creation of defective products—digital manufacturing embeds quality control throughout every stage of production. This ensures issues are detected and corrected in real time, improving efficiency, reducing waste, and delivering consistently higher-quality outcomes.
Key quality improvement strategies include:
- Continuous real-time monitoring of production parameters
- AI-powered defect detection with microscopic precision
- Automated statistical process control
- Immediate process adjustments when variations are detected
- Comprehensive data logging for traceability
Advanced machine learning algorithms can detect subtle quality variations that human inspectors might miss. For instance, in semiconductor manufacturing, digital technologies can identify microscopic defects invisible to the human eye, reducing defect rates by up to 90%.
Significant Cost Reductions and Resource Optimization
Cost reduction in digital manufacturing goes far beyond traditional efficiency measures. It represents a fundamental reimagining of resource utilization and economic efficiency.
Primary cost reduction strategies include:
- Predictive maintenance reducing equipment downtime
- Precise resource allocation minimizing waste
- Energy consumption optimization
- Reduced labor costs through automation
- Minimized inventory holding costs
What is digital manufacturing? It’s a technology-driven approach that allows companies to simulate, monitor, and optimize production processes before they happen physically. This capability leads to significant cost savings—businesses adopting digital manufacturing have reported reductions of 20–40% across various operational areas. By minimizing trial-and-error and streamlining development, digital manufacturing cuts experimental costs while boosting overall efficiency and productivity.
Let SmartOSC Guides Your Journey into Digital Manufacturing Excellence
While the benefits are clear, transitioning to digital manufacturing can seem daunting. Partnering with experienced technology providers like SmartOSC can help businesses navigate this complex transformation.
Their digital transformation approach goes beyond technology implementation, focusing on holistic business reimagination. SmartOSC provides tailored solutions that address each manufacturer’s unique challenges, including:
- End-to-end digital strategy development
- Technology architecture design
- Legacy system modernization
- Intelligent process reengineering
- Advanced operational optimization
Read more: B2B eCommerce for Manufacturers: Challenges & Solutions
Conclusion
What is digital manufacturing? It’s not just a technological upgrade—it’s a complete reimagining of industrial production. As technologies continue to converge and advance, digital manufacturing will become the standard, not the exception.
The future of manufacturing is intelligent, connected, flexible, and sustainable. Companies that embrace digital manufacturing today will be the industry leaders of tomorrow. Contact us today and take the first step towards digital manufacturing excellence.