7 Ideas For Enhancing Manufacturing Efficiency
Manufacturing efficiency is the key to success in today’s competitive and dynamic market. It means producing more output with less input, while maintaining high quality and customer satisfaction. However, achieving manufacturing efficiency is not an easy task. It requires constant evaluation, improvement, and innovation of your processes, equipment, and workforce.
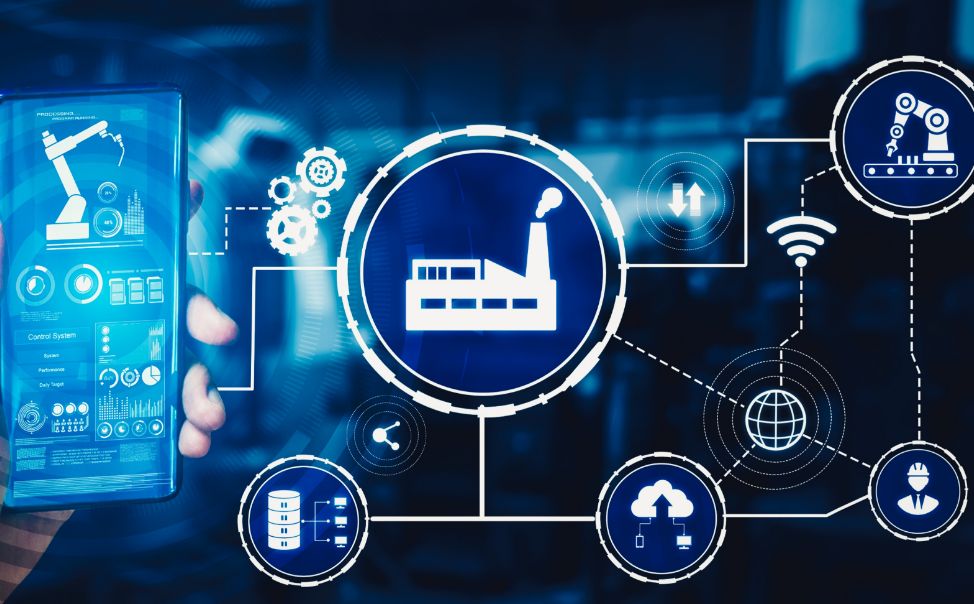
In this blog post, we will share with you seven ideas that can help you enhance your digital transformation in manufacturing and gain a competitive edge in your industry. These ideas are based on proven methods and best practices that have been adopted by leading manufacturers around the world. By implementing these ideas, you can reduce costs, increase productivity, improve quality, and boost profitability.
Idea 1: Evaluate Your Current Workflow
The first step to enhancing your manufacturing efficiency is to evaluate your current workflow and identify areas of improvement. You need to analyze how your employees, machines, and materials interact and flow through each stage of production. You also need to measure key performance indicators (KPIs) such as cycle time, throughput, yield, defect rate, and customer satisfaction. Some of the aspects that you should consider are:
- Employee skills and training: Do your employees have the necessary skills and knowledge to perform their tasks effectively? Are they trained on the latest technologies and techniques? Do they receive regular feedback and coaching?
- Production stages and bottlenecks: How many steps are involved in your production process? Are there any unnecessary or redundant steps that can be eliminated or simplified? Are there any bottlenecks that slow down or stop the flow of work?
- Technology usage and efficiency: What kind of machines and tools do you use in your production process? Are they up to date and well maintained? Do they operate at optimal speed and capacity? Do they integrate well with each other and with your software systems?
By evaluating your current workflow, you can pinpoint the strengths and weaknesses of your manufacturing process and prioritize the areas that need improvement.
Idea 2: Invest in Employee Training
Your employees are your most valuable asset in manufacturing. They are the ones who operate the machines, handle the materials, monitor the quality, and interact with the customers. Therefore, investing in employee training is essential for enhancing your manufacturing efficiency.
Employee training can help you achieve several benefits, such as:
- Online courses and webinars: These are convenient and cost-effective ways to provide your employees with access to a variety of topics and experts. You can use online platforms such as Coursera or Udemy to find courses that suit your needs.
- On-the-job coaching and mentoring: This is a practical and personalized way to help your employees learn from experienced colleagues or managers. You can assign mentors or coaches to guide your employees through specific tasks or projects.
- Safety and quality standards: This is a vital aspect of employee training that ensures compliance with regulatory requirements and customer expectations. You can use online or offline tools such as manuals, checklists, videos, or quizzes to teach your employees about safety and quality standards.
By investing in employee training, you can improve their skills, knowledge, motivation, and performance. You can also reduce errors, accidents, turnover, and absenteeism.
Idea 3: Update Your Equipment
Another idea for enhancing your manufacturing efficiency is to update your equipment with the latest technologies and innovations. Technology plays a crucial role in manufacturing, as it enables you to automate, optimize, and streamline your processes. Some of the technologies that you should consider are:
- Automated machines and robots: These are devices that can perform repetitive or complex tasks faster, more accurately, and more consistently than humans. They can also work in hazardous or difficult environments that humans cannot. Examples of automated machines and robots include CNC machines, 3D printers, cobots, drones, etc.
- Smart sensors and devices: These are gadgets that can collect, transmit, and analyze data from various sources in real time. They can also communicate with each other and with other systems via the Internet of Things (IoT). Examples of smart sensors and devices include RFID tags, barcode scanners, cameras, thermometers, etc.
- Cloud-based software and systems: These are applications that run on remote servers rather than on local computers or networks. They allow you to access, store, share, and process data from anywhere at any time. They also offer scalability, security, and flexibility. Examples of cloud-based software and systems include ERP software, CRM software, inventory management software, etc.
By updating your equipment with these technologies, you can increase your productivity, quality, accuracy, reliability, flexibility, visibility, collaboration, innovation, customer satisfaction, etc.
Idea 4: Conduct Preventive Maintenance
Preventive maintenance is a proactive approach to maintaining your equipment in good working condition. It involves performing regular inspections, checks, cleaning, lubrication, replacement, calibration, etc., before any breakdowns or failures occur. Preventive maintenance can help you enhance your manufacturing efficiency by:
- Regular inspections and checks: These are activities that involve visually inspecting or testing your equipment for any signs of wear, tear damage, or malfunction. They can help you detect and fix any issues before they become serious or costly.
- Routine cleaning and lubrication: These are activities that involve removing any dirt, dust, grease, or debris from your equipment and applying the appropriate lubricants to reduce friction and heat. They can help you prevent corrosion, rust, contamination, overheating, etc.
- Timely replacement and calibration: These are activities that involve replacing any worn-out or damaged parts or components of your equipment and adjusting any settings or parameters to ensure optimal performance. They can help you avoid breakdowns, failures, errors, etc.
By conducting preventive maintenance, you can extend the lifespan of your equipment, reduce downtime, save costs, improve safety, and comply with regulations.
Idea 5: Keep Your Manufacturing Plant Organized
Keeping your manufacturing plant organized is a simple but effective idea for enhancing your manufacturing efficiency. It involves arranging your physical space, materials, tools, and equipment in a logical, orderly, and accessible manner. It also involves maintaining a clean, safe, and comfortable work environment for your employees. Some of the methods that you can use to keep your manufacturing plant organized are:
- Implementing the 5S methodology: This is a Japanese technique that consists of five steps: Sort, Set in order, Shine, Standardize, and Sustain. It helps you eliminate any unnecessary items, arrange the necessary items in a convenient way, clean and inspect your work area, follow consistent rules and procedures, and maintain the desired level of organization.
- Using suitable handling equipment and totes: These are devices that help you move, store, and organize your materials, tools, and equipment in an efficient and ergonomic way. Examples of handling equipment and totes include pallets, racks, shelves, bins, carts, forklifts, etc.
- Maximizing space and minimizing clutter: This is a practice that involves using vertical space, modular furniture, wall-mounted boards, etc., to create more room for your activities. It also involves removing any excess or unused items, wires, cables, etc., that may cause obstructions or hazards.
By keeping your manufacturing plant organized , you can improve your workflow, reduce waste, save time, enhance quality, boost morale, and prevent accidents.
Idea 6: Reduce Material Waste
Reducing material waste is another idea for enhancing your manufacturing efficiency. Material waste refers to any raw materials, semi-finished products, or finished products that are discarded, damaged, or defective during the production process. Material waste can result from poor design, planning, execution, or control of your processes. It can also result from external factors such as market demand, customer preferences, environmental conditions, etc. Some of the ways that you can reduce material waste are:
- Adopting lean manufacturing principles: Lean manufacturing is a philosophy that aims to eliminate any activities or resources that do not add value to the customer or the product. It focuses on minimizing waste, maximizing value, and optimizing flow. Some of the lean manufacturing principles include identifying customer value, mapping the value stream, creating flow, implementing pull systems, pursuing perfection, etc.
- Applying six sigma methodology: Six sigma is a methodology that aims to improve the quality and consistency of your products and processes by reducing variation and defects. It uses statistical tools and techniques to measure, analyze, improve, and control your performance. Some of the six sigma methodology steps include defining the problem, measuring the current state, analyzing the root causes, improving the solution, controlling the outcome, etc.
- Recycling and reusing scrap materials: Recycling and reusing scrap materials are practices that involve collecting, sorting, processing, and transforming any leftover or surplus materials into new products or inputs. They help you conserve resources, reduce costs, generate revenue, protect the environment, etc.
By reducing material waste, you can increase your efficiency, profitability, sustainability, and competitiveness.
Idea 7: Automate Your Supply Chain Management
Automating your supply chain management is the final idea for enhancing your manufacturing efficiency. Supply chain management is the process of planning, coordinating, executing, monitoring, and optimizing the flow of materials, information, and money from the source to the customer. It involves various activities such as procurement, production, inventory management, distribution, logistics, customer service, etc. Automating your supply chain management means using software applications and systems to perform these activities with minimal human intervention. Some of the benefits of automating your supply chain management are:
- Enterprise resource planning (ERP) software: ERP software is a type of software that integrates all the core functions of your business into a single system . It helps you manage your finances, human resources, manufacturing operations, supply chain activities, customer relationships, etc. It also provides you with real-time data and insights to make informed decisions .
- Inventory management software: Inventory management software is a type of software that helps you track and control your inventory levels across multiple locations. It helps you optimize your inventory replenishment, avoid stock-outs or overstocking, reduce inventory costs, improve inventory accuracy, etc.
- Artificial intelligence (AI) and machine learning (ML) algorithms: AI and ML are technologies that enable your software systems to learn from data and perform tasks that normally require human intelligence. They help you automate your supply chain activities such as demand forecasting, inventory optimization, order fulfillment, delivery routing, etc. They also help you improve your supply chain performance by providing you with predictive analytics, prescriptive recommendations, anomaly detection, etc.
By automating your supply chain management, you can enhance your speed, accuracy, visibility, collaboration, responsiveness, and customer satisfaction.
Conclusion
Manufacturing efficiency is a vital factor for achieving success in the modern manufacturing industry. It can help you reduce costs, increase productivity, improve quality, and boost profitability. In this blog post, we have shared with you seven ideas that can help you enhance your manufacturing efficiency.
We hope that these ideas will inspire you to take action and improve your manufacturing efficiency. If you need any assistance or guidance in implementing these ideas, please feel free to contact us at SmartOSC. We are a leading cloud solutions provider that can help you with digital transformation in manufacturing. We can help you design, develop, deploy, and manage cloud-based solutions that suit your specific needs and goals.